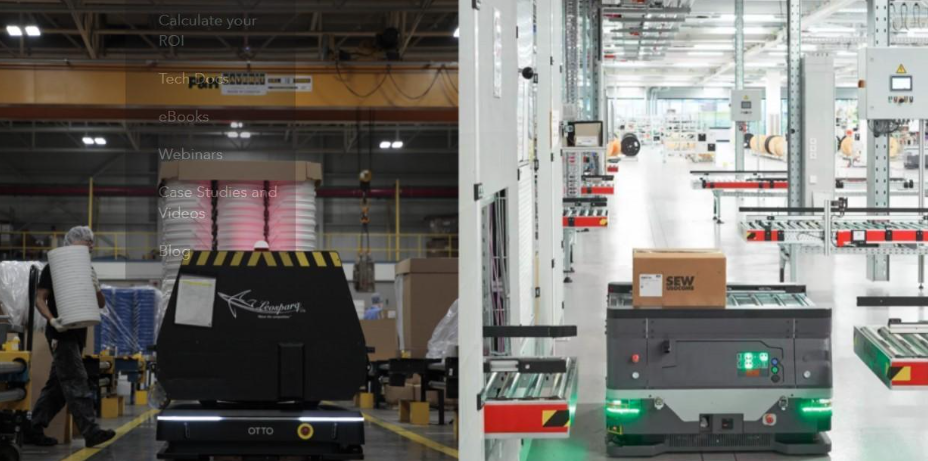
In December 2022, OTTO Motors hosted “The Best of Both Worlds: Unlocking the Productivity of AGVs and AMRs”: a webinar that analyzed the differences between AMRs and AGVs, from their technology to their applications. This webinar introduced the idea of Graph-based Planning, an algorithm that enables manufacturing facilities to achieve the benefits of both AMRs and AGVs in one robot, including the predictability of AGVs alongside the flexibility of AMRs.
[In case you are new to material handling automation, AMR stands for Autonomous Mobile Robot and AGV stands for Automated Guided Vehicle. You may want to read this blog post first to learn more about the differences between the two vehicles, and then return here to finish this blog.]
Despite their differences, AMRs and AGVs need to work together in the future, in the same facilities. Although they utilize different technologies and will be used for different applications and workflows, their unique benefits complement each other well. Interoperability holds the key to the success of this advancement.
“Interoperability is really a term that we mean to allow dissimilar robots to occupy the same space intelligently. So, this means communicating with one another to share information about where they are [and] what their intentions are to allow them to be good citizens and share the space collaboratively.”
— David Northup, Director of Product Management, OTTO Motors
OTTO Motors and InOrbit demonstrated interoperability between an AGV and an AMR at the AMR Conference in October 2022 by showing how the two robots can work together. This was facilitated by a new open source VDA 5050 to ROS2 connector developed in part by the two companies.
In addition to interoperability, here are five expectations for the future of AMRs and AGVs working together.
1. AMRs and AGVs Will Only be Differentiated Through Path Planning Options
As material-handling robots like AMRs and AGVs become increasingly similar, their main differences will be between path planning options. Some AMRs will retain Search-Based Path Planning, which is similar to an ATV in a field. The ATV has no prescribed path and can take whichever route is most efficient to its destination. Moreover, some AGVs will continue to act like a train on a track, following a specific path and unable to deviate from it when an obstacle blocks the route.
On the other hand, some material handling robots will use Graph-Based Path Planning, which acts like a car on a road. The car will use prescribed paths to get to the destination but can deviate from the path when something blocks the route. This results in some AMRs becoming increasingly predictable as some AGVs become increasingly flexible.
2. Similar Communication Standards Will Govern Both AMRs and AGVs
Recent efforts in the material handling industry have produced attempts at standardizing communication protocols between robots from dissimilar vendors and dissimilar types, such an AGV versus AMR. Primarily, this is motivated by no single vendor having a large enough fleet of robots and capabilities that can address the diverse and growing set of needs that a typical large-scale manufacturing facility or warehouse may have.
Thus, through communication standardization, the industry hopes to facilitate the interaction of these unique robots, and improve efficiency and safety through centralized coordination. OTTO Motors is taking an open approach to this challenge by investing in and contributing to open-source efforts that benefit the industry as a whole. The robots that do not comply with these emerging standards will be at a disadvantage in the industry.
3. Standards Will Shape and Be Shaped by the Market
Historically, most AGVs and AMRs only worked with their own specific fleet management software. This puts an unnecessary burden on end users that operate dissimilar robot types to adapt or create their own means of communication between their robots. Failure to work out this issue resulted in a host of interoperability issues and a difficult deployment. Sometimes completely separate paths needed to be created, causing a loss in facility space.
Today, the market is moving toward communication standardization. Larger users of diverse robots are especially interested in having a fleet management system capable of operating their fleet.
“Once a customer is fully invested in a specific robotic Fleet Manager, it is difficult to divest from that infrastructure and explore alternatives. This is why ELT Systems Group, along with OTTO Motors, is exploring ways to allow customers to be flexible and not be locked into potential legacy manufacturers when the industry is advancing so quickly.”
— Jason Dodge, Automation Manager, ELT Systems Group
VDA 5050, a standardized interface for AGV and AMR communication, was actually born out of the automotive manufacturing industry, one of the largest users of material handling robots in the world. Increasingly, however, this market need is encompassing all industries as robotics vendors worldwide learn to work together.
4. There is a Proliferation of Third-Party Fleet Management Solutions
Today, AMRs and AGVs are still primarily designed for use in fleets of robots from the same vendor and of the same type. This will continue to be the primary use case and most efficient deployment style for the foreseeable future, since each vendor is best equipped to manage fleets of their own robots.
With the advent of interoperability standards, there has been an emergence of third-party fleet management solutions that aim to direct communication, coordination and control of fleets that include heterogeneous robot types and vendors. These systems are currently only capable of basic communication and control, but over time, they will evolve to become more advanced and powerful.
“[Interoperability enables] different robots from different vendors working together to complete a more advanced mission.”
— Florian Pestoni, CEO, InOrbit
5. Location Tracking Systems Will Improve for Better Coordination and Safety
Location tracking systems provide manufacturing facilities a mechanism for establishing a global tracking reference for any object that a facility manager needs to locate.
In an ideal world, an AMR or AGV would have full awareness of all other moving objects within their operating domain, including humans and other manually operated machines such as a forklift. With this global knowledge, they would be able to respond both reactively and proactively to the objects they are encountering. Currently, however, robots are only able to reactively respond when they encounter an obstacle.
As location tracking systems improve, robot fleet managers will know the location of a manually operated forklift or human, for example, that may be blocking an aisle way on the future path of a robot. Then, the fleet manager could use this awareness to alert the AMR in advance, allowing the robot to proactively plan an alternative route to its destination that is more efficient, coordinated, and safe.
We’d like to thank OTTO Motors’ David Northup, and InOrbit’s Florian Pestoni for their assistance in preparing this blog post. Their insights into this innovative industry have been very helpful.
In closing, we see the robotics industry continuing to evolve to meet new consumer needs and market trends. Although AGVs and AMRs still have distinct technology differences and application uses, the not-so-distant future will see material handling robots collaborating in manufacturing facilities throughout the world.
Interested in learning where to start?
Download this white paper: 8 Key Considerations When Assessing Autonomous Mobile Robot Vendors. Then contact ELT Systems Group. As an OTTO Certified Dealer, our automation experts welcome the opportunity to review your automation project. Please reach out to our team to start a conversation.