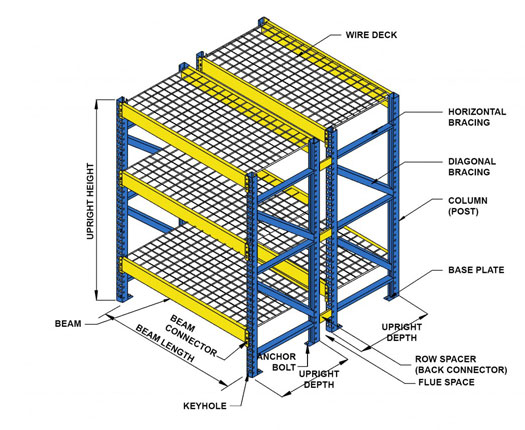
Pallet racking has been around for many years. In the early 1900s, when forklifts were first introduced, businesses quickly realized they could gain more valuable storage space by expanding vertically (as opposed to extending their building horizontally) and place products and materials in racks.
In the past few decades, as e-commerce has changed the face of business and 1,000,000+ square-foot warehouses have become commonplace in the U.S., pallet rack is often taken for granted. It shouldn’t be overlooked. Let’s take a minute to review the basic rack componentry.
So, what exactly is pallet rack?
Pallet rack is composed of upright frames, beams, braces, support bars and footplates, assembled together to create rows, bays, and levels of pallet storage. These structures are normally serviced by forklift truck operators.
As the name implies, upright frames are the vertical component of the system. They may be made of cold “roll-formed” steel or hot-rolled “structural channel” steel. Roll-form upright frames are most common. They are lightweight, yet exceptionally strong, durable and great for selective rack designs. Structural channel upright frames cost a bit more money but provide extra strength for drive-in rack, pallet flow and high-density rack systems. Upright frames are typically made up of two columns that are braced together.
Beams, are known by a variety of terms such as load beams, step beams, box beams, and channel beams. They provide the horizontal structural element and the beam length equals the bay width or clear opening. When mated with a roll-form upright frame, the load beam connects via a safety lock, aka safety clip. Load beams connect to structural channel systems via bolts and a connector plate.
Pallet rack also incorporates horizontal and vertical braces for support.
Support bars extend between and connect two load beams. They provide the support underneath the stored load (pallets). Wiring decking provides additional support and prevents loose objects from falling.
Footplates, also called baseplates or footpads, are bolted down, to anchor the upright frames into the floor. Sometimes shims are needed with uneven floors. Shims may be welded together so long as the overall size does not exceed 6x the maximum bolt diameter.
Are you in need of pallet rack or just have some questions? Either way, we encourage you to contact the ELT Systems Group. We work with pallet rack every day, quoting, designing, installing and repairing all different types of rack and shelving systems in all kinds of applications. Call (888) 779-8880 and ask for the ELT Systems Group.
In a future blog post, we will take a look at the different types of rack systems and other terminology.