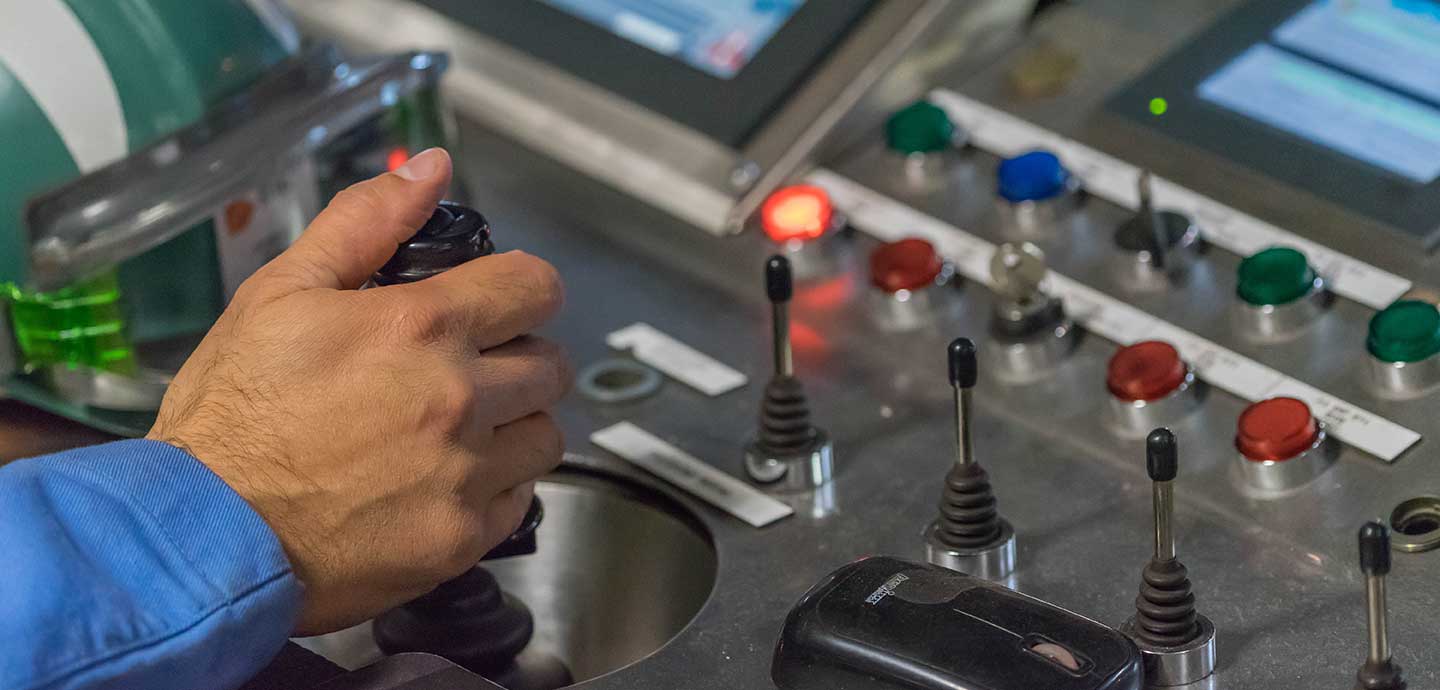
It’s a new era for warehouse and material handling automation and robotics and that means there are solutions for all different sizes and scope of operations. Many warehouses have been working with the same equipment and infrastructure for so long that layers of design and need have evolved over decades leaving operations potentially in-efficiency and in serious need of an upgrade. Here are some signs that may signify that automation and/or robotics may be a solution to improving your operations.
High Turnover Rates
If you find that your facility is constantly searching for new associates to operate equipment AMRs (autonomous mobile robots) may be a solution to look in to. These come in forms of automated tuggers and fork trucks or even mobile platforms. If your facility operates at least 2-3 shifts a day, then a target ROI of 2-3 years may be achievable.
These robots will allow the valued associates on your team to stay in aisle doing picks and puts and making the robotic equipment do the horizontal transport. Think of these robots as mobile conveyor systems. This will result in increased picking and put times allowing associates to work smarter and not harder.
High Cycle Times or Low Pick Velocity
If you find that your picking velocity is low or the cycle time in pick and puts of full pallets is high that different automation and robotic solutions are available for consideration. Pick to Light systems can help you achieve faster and more accurate picks for kitting and e-commerce operations. This removes paper lists and reading bill of materials for orders and instead react to lit panels under bins to retrieve items.
In addition to Pick to Light robotic solutions like explained above also increase these metrics. Other robotic solutions offer mobile platforms that travel to picking solutions and allow associates to pick orders as robots come to them rather than retrieving stacks of orders from a central location.
Zero Capacity and New Building Expansion
If you’re one of the many companies that are looking to expand your warehouse, lease new property or looking to move into a new building there are a handful of new automated solutions that help you reduce your existing racking footprint and automate full pallet in and out operations. Automated pallet shuttles that can move three dimensionally; left, right, back, forward and up and down can really condense your storage space where your aisle widths are now just the width of a single pallet instead of needing room for a manual truck.
This solution allows pallets to be called automatically to a pick up location via conveyor and you can also automatically put pallets away as well increasing efficiency and throughput in your operation. The savings from expansion and leasing are easily put into an ROI calculation.
Not only is a pallet shuttle a great solution so are others like VLMs and mobile racking. Both are more conventional solutions but ultimately save you space and increase your pallet positions.
Aging Conveyor Systems
If your conveyor systems are decades old then certainly downtime, energy efficiency and the loudness of your systems are some concerns that you already have. While your operations may changed and built around an older installation or maybe your business model changes and you need to be more nimble, you may want to check out how new conveyor technology while considering a new layout. You may want to also consider integrating conveyors with automated packing, wrapping and palletizing systems to further streamline your operation.
These are only a few different signs that you may be ready for a technology upgrade and only a few different solutions. Reach out to ELT Systems Group to set up a call and we can review a large selection of solutions that may be a perfect fit for your operational upgrade.
Contact the systems group today or Jason Dodge directly for further information and to get started on your project today.
Jason Dodge
Automation Manager | Systems Division
Eastern Lift Truck Co., Inc.
Cell: (609) 605-1043
Email: jdodge@easternlifttruck.com